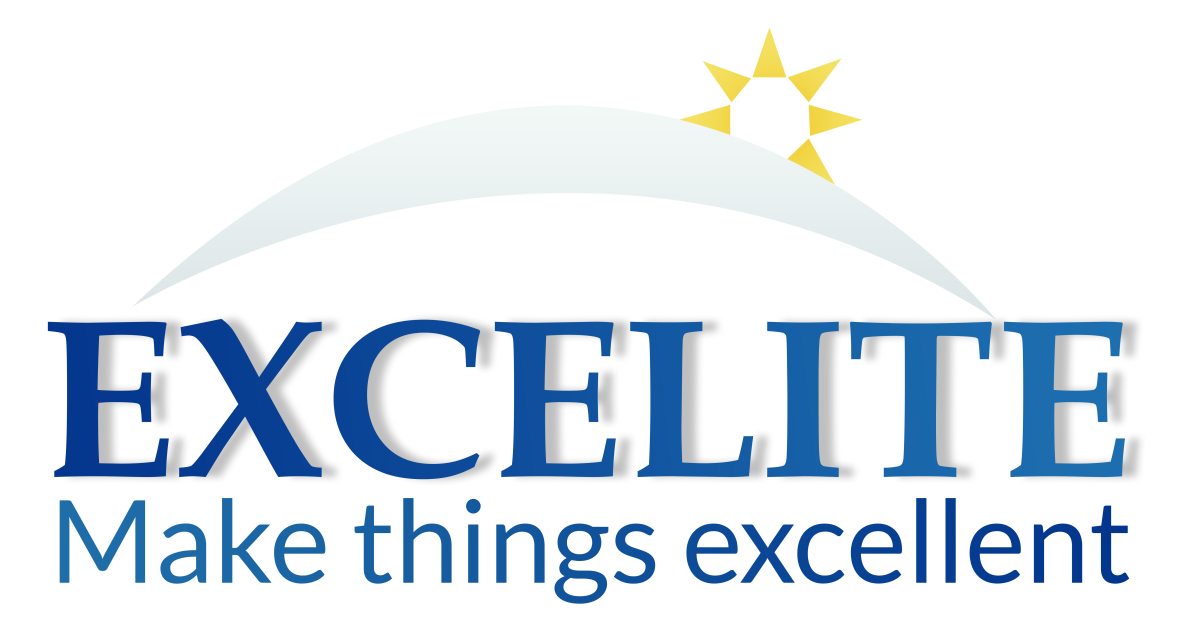
- HOME
- POLYCARBONATE
- ACRYLIC
-
-
- ACRYLIC SHEETS
- Clear Acrylic Sheets
- Cast Acrylic
- Tinted Acrylic Sheets
- Anti-Fog Acrylic Sheets
- Acrylic Mirror Sheet
- Translucent Opal Acrylic Sheet
- Anti-Static Acrylic Sheets
- Anti Reflective Acrylic Sheets
- Anti-Graffiti Acrylic Sheets
- Anti-Glare Acrylic Sheets
- Fluorescent Acrylic Sheet
- Red Acrylic Sheet
- Opal & Matte Acrylic Sheets
- Opal Acrylic Sheet
- Matte White Acrylic Sheet
- Matte Black Acrylic Sheet
- ACRYLIC SHEETS
-
-
- FABRICATION
- APPLICATION
- BLOG
- ABOUT US
- CONTACT US