Unlock the Secrets of Printing on Plastic Sheets: Your Comprehensive Guide
Embark on a journey of knowledge with our comprehensive guide to printing on plastic sheets. Whether you’re working with acrylic sheet, polycarbonate sheet, or PVC sheets, discover the right techniques for each, from UV printing on acrylic to digital printing and silk screen printing on acrylic or polycarbonate. Whether you’re a DIY silk screen design or seeking professional printing services, this guide provides valuable insights to ensure precision and clarity on plastic surfaces.
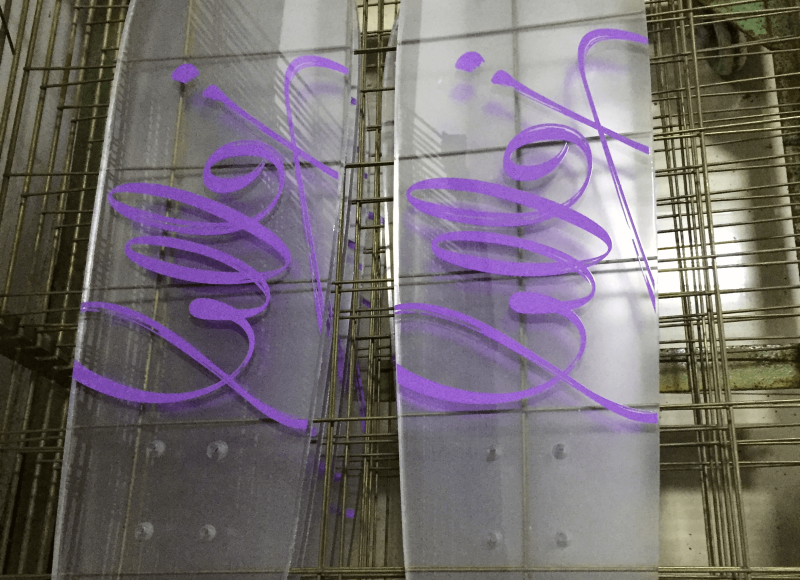
You may want to add custom graphics to your acrylic sheets or polycarbonate sheets or polycarbonate films. Printing on plastic sheet, printing on glass, printing on acrylic is very popular in many application.
Types Of Printing On Plastic Sheet
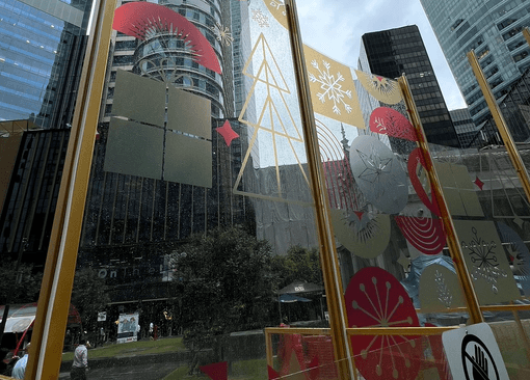
1. Screen printing on Acrylic or polycarbonate
Screen printing involves utilizing a mesh screen, ink, and a squeegee to transfer a stenciled design onto acrylic sheet or polycarbonate sheet surface. The most popular materials for screen printing are fabric and paper, but you may also print on metal, plastic, glass, and wood using specialty inks. The basic process is making a stencil on a fine mesh screen, which you then push ink (or paint, for posters and artwork) through to imprint your image on the surface below.
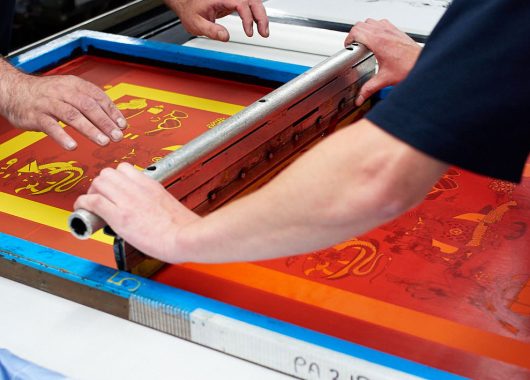
Silk screening, often called silk screen printing or screen printing, might differ based on the materials used to form the stencil, but the actual printing process is always pretty much the same. Various methods of stenciling include:
- Covering the targeted portions of the screen with vinyl or masking tape.
- Add adhesive or lacquer as “screen blockers” to the mesh to paint the stencil.
- Making a stencil using a light-sensitive emulsion and developing it similarly to how a photograph is produced.
Designs created with the screen-printing method can use multiple ink shades or simply one. When applying color to items with many colors, use different stencils for each ink and apply the colors in isolated layers.
2. Digital printing on Acrylic or polycarbonate
Digital printing is a modern method where a computer creates designs and a special printer quickly dries the ink using UV light. This technique works on various surfaces like paper, metal, glass, acrylics, ceramics, or wood, as long as it fits in the printer. It’s a fast and efficient way to bring designs to life on different materials
Digital printing on acrylic and polycarbonate surfaces marks a transformative approach to visual communication. This cutting-edge method allows for precise reproduction of digital designs directly onto these transparent materials. Whether you seek vibrant signage, intricate patterns, or personalized graphics, digital printing offers unparalleled flexibility and detail. Explore the benefits of this advanced technique, including rapid production, high-resolution prints, and the ability to bring designs to life on acrylic or polycarbonate surfaces. Elevate your projects with the clarity and precision that digital printing on these materials can provide.
Why Print On Acrylic Sheet Or Polycarbonate Sheet?
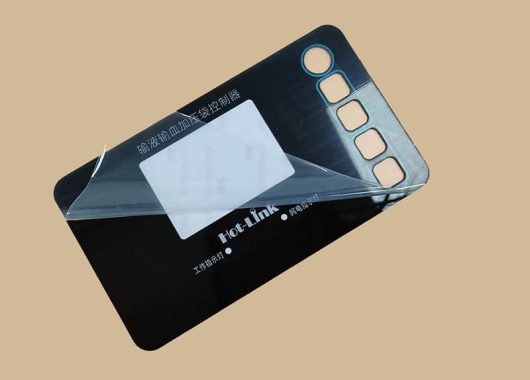
Polycarbonate sheet is stronger than acrylic sheet, offering durability and strength. Excelite plastic employs various fabrication methods, including screen printing, UV printing, thermoforming, polishing, cut to size, drilling, and CNC routing. Both materials can be fabricated for diverse signage applications.
With options for clear sheets in various sizes and thicknesses, polycarbonate and acrylic are suitable for sign faces, display panels, POP displays, individual cut letters, and other graphic and architectural elements. At the Excelite Fabrication Center, we provide a comprehensive one-stop solution for all your polycarbonate or Acrylic related product needs.”
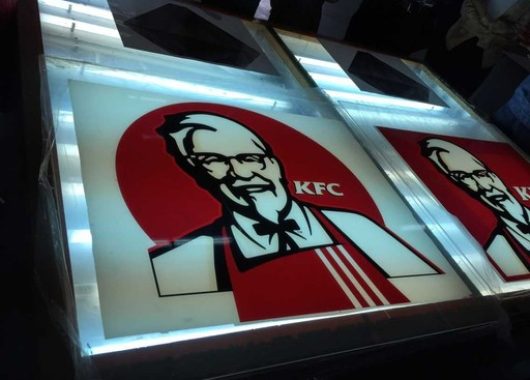
Outstanding Strength
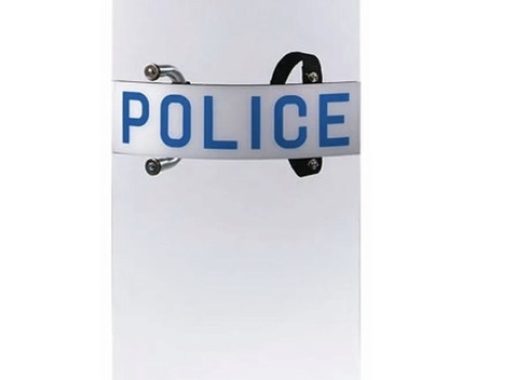
Due to its flexibility, polycarbonate may bend without cracking or displaying stress fractures. It’s the ideal choice in situations where impact resistance counts.
Polycarbonate printers often print images mirroring the material’s back (second surface). Since the material substrate is transparent, the printed graphic is visible only when the material is printed in reverse.
Regarding POP displays, graphic overlays, or industrial labels—where the general public and potential vandals may touch or poke—the substrate serves as the ink’s shield. This is why reverse prints on polycarbonate last much longer than first surface prints.
Versatility
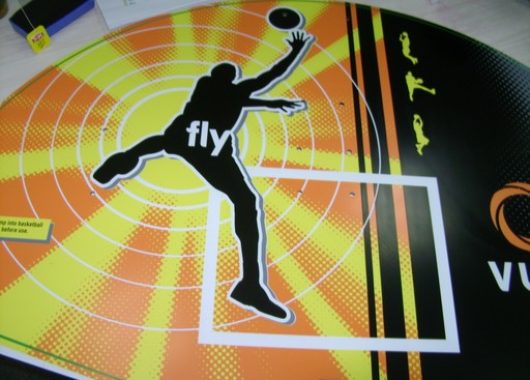
Many Available Options
Cost-Efficiency
Polycarbonate is more expensive than other transparent polymers like PETG or acrylic. Nevertheless, there might not be a good substitute that can match the longevity of a PC, depending on the application (overlay graphics, for example).
According to the application, these materials must be heat-bent occasionally and die-cut at thin and thick gauges while searching for printed signs and shop display solutions. Polycarbonate is simple to work with and finishes quickly.
Quality
Polycarbonate screen printing produces high-quality results. The screen-printing machines now provide a greater color palette and better color saturation.
More pigments are used in thicker ink applications to polycarbonate materials than in digital printing, producing richer, more dazzling colors.
Additionally, serigraphy allows for adding unique colors and unusual effects to the polycarbonate printing process.
Durability
A Variety Of Applications to Silk Screen Printing
- Packaging and Labels: Silk printing is widely used in packaging and label design due to its ability to produce high-quality, weatherproof designs.
- Signage and Banners: Silk screen printing to signage and banners made from plastic materials, where it can be used to create durable and visually appealing graphics .
- Fine Art Prints: While primarily associated with fabric and paper, silk screen printing can also be applied to plastic surfaces. This application is less common but offers unique opportunities for artists to create innovative and durable fine art prints on unconventional substrates .
- Product Decorations: Silk screen printing is an excellent option for product decoration on plastic items. It is compatible with most plastic manufacturing processes such as injection molding and thermoforming, making it versatile for various product shapes and sizes .
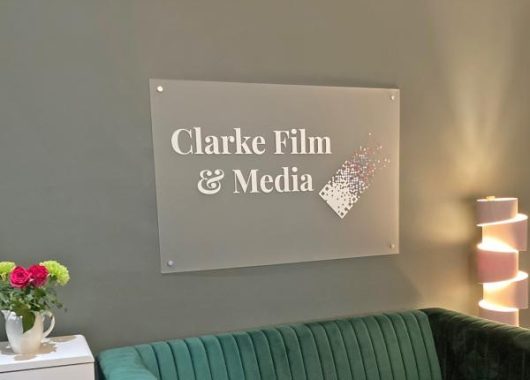
How Does Screen Printing Work?
Step 1: Design Development
Making the design is the initial step in the screen-printing procedure. After a design is selected, it is printed onto a film made of clear acetate, which is subsequently used to make the stencil or screen.
Step 2. Choosing and Setting Up the Screen
After completing the design, you must choose the screen and mesh count. One square inch’s worth of fibers is known as its mesh count. The design being printed will determine which mesh count you require.
Low mesh screens allow ink to flow through because of their broader apertures, while higher mesh screens print finer details while maintaining a decent ink coating.
Following selection, a coating of light-reactive emulsion is applied to the mesh screen.
Typically, emulsions come in three primary varieties:
• Diazo: Less expensive; requires a more prolonged exposure; unsuitable for finely detailed prints.
• SBQ-based: Requires no mixing, heals very fast, is costly, and is appropriate for intricate work.
• The third type of emulsions is called dual-cure, which combines Diazo and SBQ. It is less expensive than SBQ and takes less mixing time than Diazo.
Step 3. Getting the Emulsion Out
The emulsion hardens and develops when the transparent acetate film is carefully put on the mesh screen coated with emulsion and exposed to bright light. Using distinct screens for each color is crucial when using several colors.
Step 4: Making Stencils
The screen will become more complex in the exposed portions after a predetermined time, and any unhardened emulsion will be washed off to leave a clean imprint. After the screen has dried, the printer will perform any necessary touch-ups to ensure the imprint is as close to the original. It is now possible to use the stencil.
Step 5. Preparation for Print
When the material is ready to print, it is laid flat on the printing board, and the screen is positioned in the desired direction.
Step 6. Applying the Design
This step will bring the printed design to life. It is crucial to lower the screen to reach the printing board. The top of the screen has the desired ink color. A squeegee will spread the ink evenly over the screen’s length. The design is printed on the product due to the ink seeping through the stencil’s exposed sections and transferring to the silk underneath.
After everything is printed, the stencil will have served its job. Removing emulsion from the mesh using a unique cleaning solution can help make stencils.
Step 7. Heat Curing & Finishing
The printed product is heat-cured through a dryer to achieve a smooth design. This helps to prevent the design from fading.
How is Screen Printing Different from Digital Printing?
Screen printing and digital printing are distinct techniques in the world of printing Acrylic and printing polycarbonate.
Screen printing involves pushing ink through a mesh or screen to transfer the design onto plastic sheet surface. It’s ideal for large-scale projects and works well on various materials, providing vibrant and durable results and cost friendly.
Digital printing, on the other hand, utilizes computer-controlled printers to reproduce digital images directly onto surfaces. This method is versatile, allowing for customization and variable data printing. It’s suitable for smaller print runs and offers high-resolution results.
In summary, while screen printing is traditional, manual, and suitable for larger quantities, digital printing is modern, computer-controlled, and excels in customization for smaller quantities.
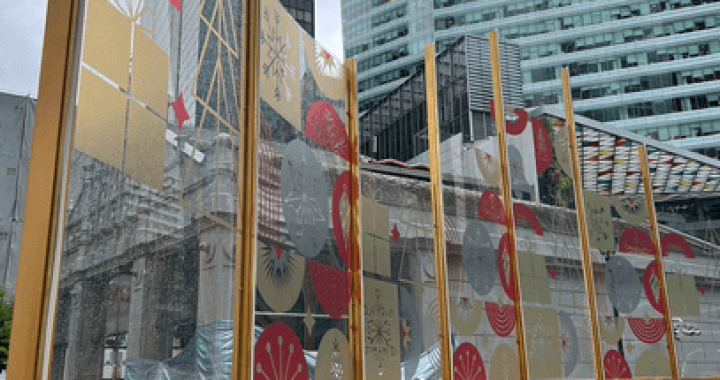
Is Screen Printing Cheaper Than Digital Printing?
The Basic Differences Between Screen Printing & Digital Printing
Screen printing and digital printing are two common methods used for transferring images onto different surfaces.
Screen printing involves using stencils to apply ink layers through a mesh screen, while digital printing utilizes computer-controlled printers to directly transfer images onto materials.
Screen Printing is Ideal for simple designs with solid colors. Each color in the design requires a separate screen, which can limit the number of colors used.
Digital Printing offers a wide range of color options and allows for intricate designs with gradients and detailed imagery without the need for separate screens.
Speed And Delivery Time For The Two Printings
Screen Printing is slower than digital printing due to the time-consuming process of creating and aligning screens for each color. Not ideal for rush orders.
Digital Printing is faster turnaround time as the printing process is computerized and does not require extensive setup. Suitable for quick production and on-demand printing.
The Bottom Line
Get A Quote Today
Bring Your Ideas to Life with Excelite Plastics.
Custom Polycarbonate Solutions Tailored for You.
Share Your Project With Us!
+86 135 8555 4902