Thermoforming Polycarbonate Everything You Need to Know
Thermoforming polycarbonate is a manufacturing process involving the heating of polycarbonate sheets until they become pliable. Once in this flexible state, the sheets are formed or shaped using molds or patterns to create various products such as domes, containers, or specific parts for different applications.
1. Is polycarbonate thermoplastic?
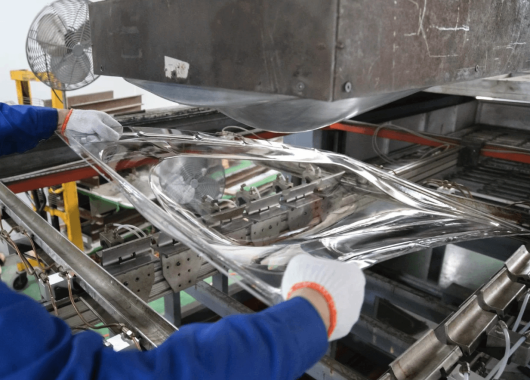
Polycarbonate sheet is a great thermoplastic material. Polycarbonate maintains its properties over a wide range of temperatures, from -20 to 140°C, polycarbonate melting temperature is 155°C, it will become soft, and then can be thermos molded or heat formed into various shapes. Polycarbonate can be heated and reshaped multiple times without significant chemical changes. This makes polycarbonate suitable for processes like thermoforming, vacuum forming, drape forming, press forming, where it can be heated, moulded, and cooled to create desired shapes.
The approach used to forming polycarbonate sheets varies based on polycarbonate sheeting thickness, the shape of the product you want to achieve, and the complexity of the job. If you want to do simple straight-line polycarbonate bending, a heat gun can do the job.
If the polycarbonate sheet thickness is less than 5mm, you can easily be thermoformed using a one-sided heater machine. However, for demanding applications involving complex products or super thick polycarbonate sheets, it takes a longer time to heat the sheet. To ensure even heating, using two-sided heated machines or thermoforming oven is recommended.
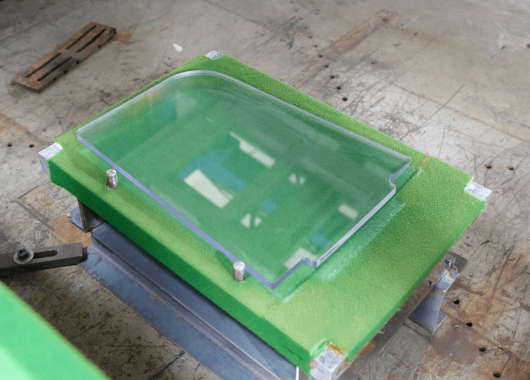
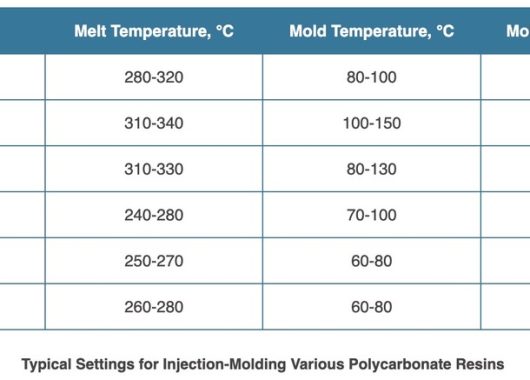
2. Main Types of plastics for thermoforming
Thermoforming plastic is a flexible manufacturing process utilized with different types of thermoplastic materials. Selection of thermoforming plastic relies on factors like the desired product properties, its intended application, and cost factors. Here are several primary thermoplastic materials frequently employed in thermoforming:
Polystyrene (PS):
Polystyrene is a widely used thermoplastic known for its clarity and ease of thermoforming. It is often used for packaging materials, disposable cutlery, and various consumer products.
Polyethylene (PE):
Polyethylene comes in two main types, low-density polyethylene (LDPE) and high-density polyethylene (HDPE). LDPE is flexible and used for items like plastic bags, while HDPE is more rigid and used for bottles, containers, and pipes.
Polypropylene (PP):
Polypropylene is a versatile thermoplastic known for its heat resistance and chemical resistance. It is used for packaging, automotive components, and consumer goods.
Polyvinyl Chloride (PVC):
PVC is known for its rigidity and chemical resistance. It’s used for applications such as pipes, fittings, vinyl siding, and blister packaging.
Acrylonitrile Butadiene Styrene (ABS):
ABS is a strong and impact-resistant thermoplastic often used in the automotive industry for interior and exterior parts, as well as in consumer electronics.
Polycarbonate (PC):
Polycarbonate is transparent, strong, and heat-resistant. It’s commonly used for applications requiring optical clarity, such as eyeglass lenses, as well as for safety equipment, electronic enclosures, and automotive components.
Polyethylene Terephthalate (PET):
PET is used for packaging, particularly in the form of PET bottles for beverages and other liquids. It offers good transparency and is recyclable.
Polymethyl Methacrylate (PMMA):
PMMA, commonly known as acrylic, is used for applications requiring optical clarity and weather resistance, such as display cases, signs, and lighting fixtures.
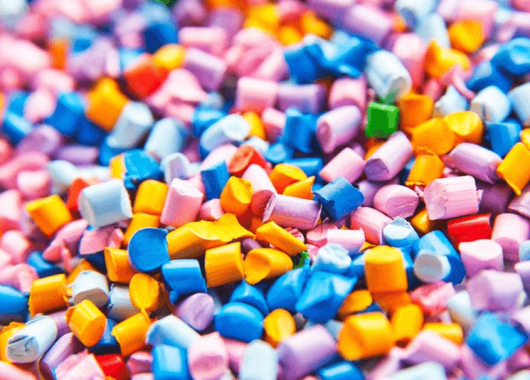
3. The main techniques used in polycarbonate thermoforming
Perspex sheets are easily thermoformed, and a wide variety of applications can be produced using the process. When combined with CNC routing, printing, bonding, and polycarbonate coating, even more complicated products can be created from polycarbonate sheeting and Acrylic sheeting.
The basic steps for thermoforming involve plastic sheet heating, shaping, cooling, and finishing. There are several different forming techniques, some of which only require heating to allow the plastic sheet to conform to a simple positive or negative mold, as in drape forming or both positive and negative mold as mechanical forming. Others, such as vacuum and pressure forming, require that, after heating, the sheet is made to conform to a mold by applying pressure or a vacuum.
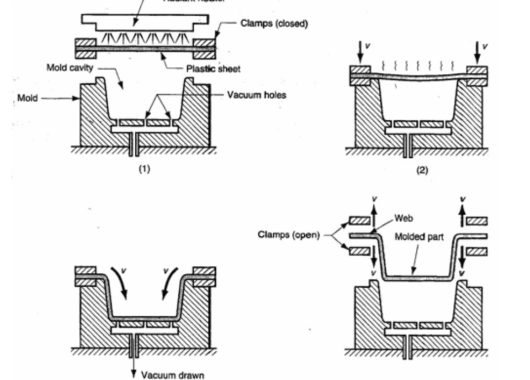
4. The most common polycarbonate thermoforming techniques
- Vacuum Thermoforming
- Pressure Thermoforming
- Mechanical Thermoforming
- Drape Forming
- Blow Forming
We will go through these thermoforming processes one by one to help you choose the best processing way for your product.
Vacuum thermoforming
Vacuum thermoforming is a plastic fabrication technique used to shape thermoplastic sheets into three-dimensional forms. Vacuum thermoforming involves heating thermoplastic sheets to a pliable temperature, forming them to a specific shape using a mold, and then trimming to create a finished product. When the part is formed to the mold, vacuum pressure is added to assist with the molding of the part.
As a highly mature thermoforming technique, vacuum forming has been widely applied. Its advantages include low mold processing costs, short production time, and high production efficiency. Vacuum thermoforming does not produce exhaust gas, wastewater, or waste, meeting environmental requirements. It can create various irregular shapes and is suitable for mechanised and automated packaging, saving labor.
Moreover, thermoforming vacuum forming can create super-large and more complicated shapes. For example, when creating a polycarbonate igloo, the largest panel can measure 2.1m x 5.5m in a single piece.
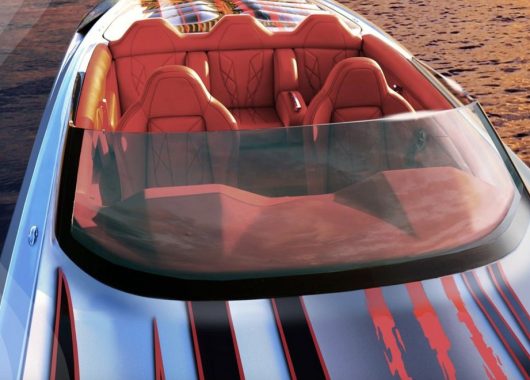
How vacuum thermoforming is Done
During vacuum thermoforming, excess moisture can cause bubbling and other surface appearance defects as well as a reduction in property performance. Whilst the amount of water absorbed is not significant compared to other hygroscopic materials, it is essential that it is removed prior to forming. A hot air-circulating oven at 125°C ± 3°C is recommended. To avoid warpage, drying temperatures should not exceed 125°C and the air volume in the oven should be changed six times per hour to allow for the removal of water vapour. Overheat may cause bubble too.
The process of vacuum thermoforming involves several steps:
Material preparation: Almost all thermoplastics have moisture absorption, with polycarbonate having a water absorption of 0.1% (WT). During vacuum thermoforming, excess moisture can cause bubbling and other surface appearance defects, as well as a reduction in property performance. While the amount of water absorbed is not significant compared to other hygroscopic materials, it is essential to remove it prior to forming.
Drying the material: A hot air-circulating thermoforming oven at 125°C ± 3°C is recommended for drying the polycarbonate panels to remove moisture. To avoid warpage, drying temperatures should not exceed 125°C, and the air volume in the oven should be changed six times per hour to allow for the removal of water vapor. Overheating may cause bubbling as well.
Heating the material: Once the polycarbonate sheeting is dry, it is heated to a pliable temperature. Uniform heating is vital for achieving a consistent and high-quality final product. The heating temperature varies depending on the polycarbonate material and thickness.
Forming the material: When the plastic sheet reaches the appropriate pliable temperature, it is placed over the mold. Vacuum pressure is then applied to assist with molding the sheet to the desired shape.
Cooling: After the plexiglass sheet has conformed to the mold, it is cooled to solidify and hold its new shape. The cooling process should be controlled to optimise the final product’s quality and reduce possible stress or warpage.
Trimming and finishing: Once the formed polycarbonate sheet has cooled, we will offer 3 or 5 axis CNC trimming or laser cutting.
By following these steps, vacuum thermoforming can successfully create a wide variety of three-dimensional forms from polycarbonate sheets, ranging from simple shapes to highly complex and large-scale designs.
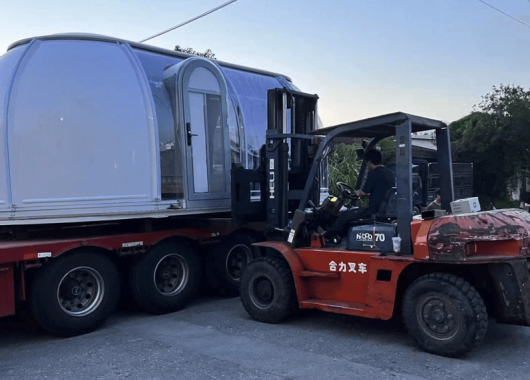
Do you need peel the protective film off during thermoforming?
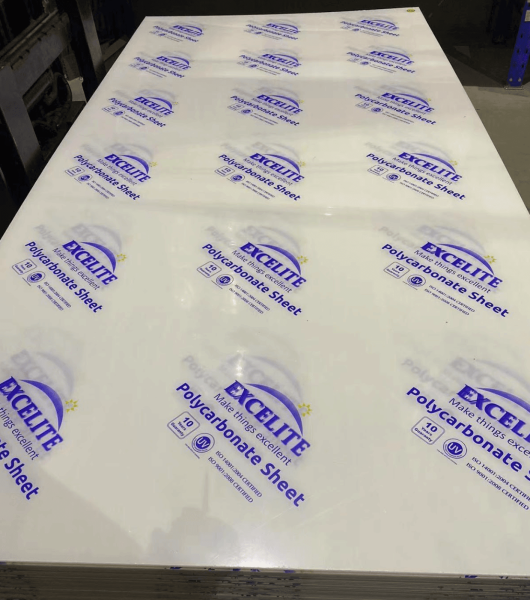
Thermoforming processing
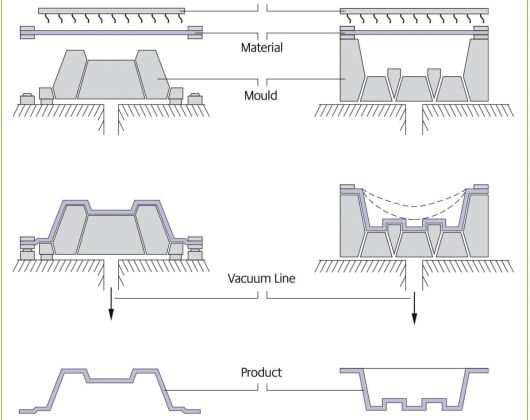
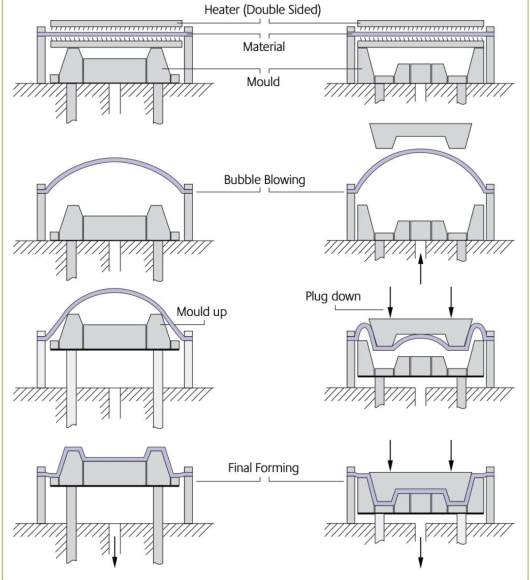
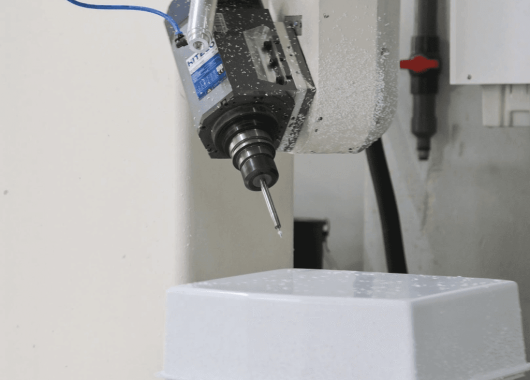
Some other details you may should pay attention to
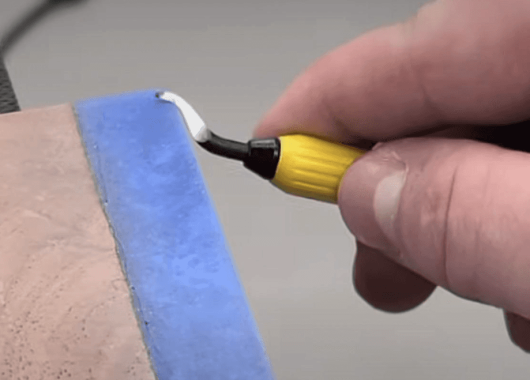
Benefits of vacuum thermoforming
Applications for vacuum thermoforming
- Polycarbonate kayaks
- Polycarbonate igloos
- Polycarbonate suitcases
- Police shield
- Machine guards
- Boat windshield
- polycarbonate windshield
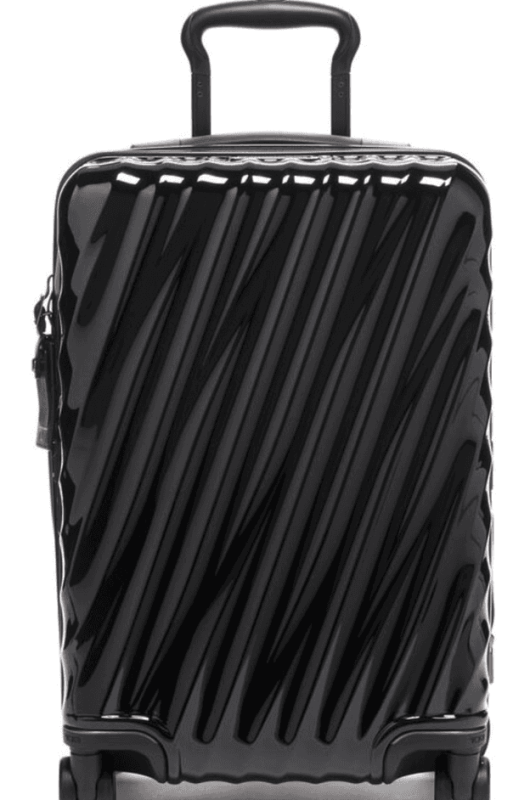
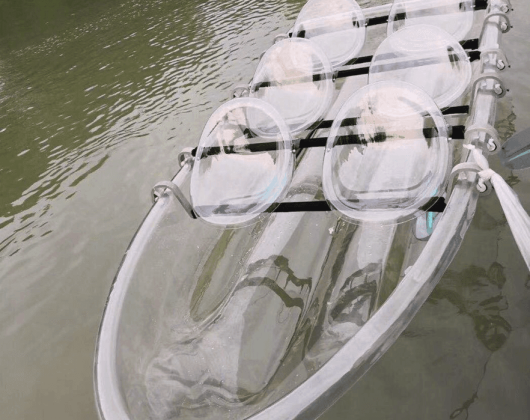
Pressure Thermoforming Polycarbonate
Here's how pressure thermoforming typically works:
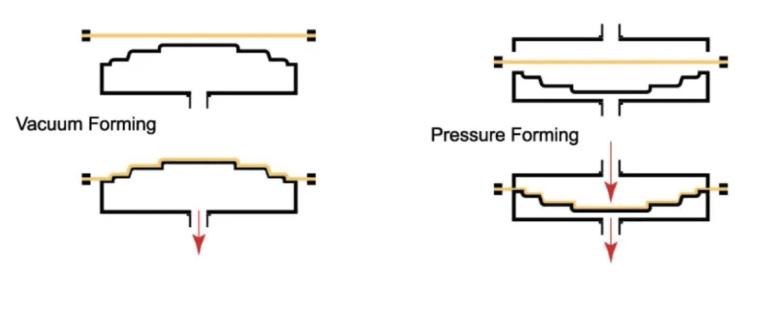
- Heating: A thermoplastic sheet is first heated to a specific temperature, typically just below polycarbonate melting point. This makes the material soft and pliable, making it easier to shape.
- Forming: The heated sheet is then positioned over a mold or tool, which has the desired shape of the final product. A combination of vacuum and pressure is applied to the sheet. The vacuum helps to draw the sheet tightly against the mold to capture its shape, while pressure (either through air or mechanical means) is applied to force the material into the intricate details and fine features of the mold.
- Cooling: Once the thermoplastic material has taken the shape of the mold, it is cooled rapidly. This cooling process solidifies the material, ensuring that it retains the desired shape when removed from the mold.
- Trimming: After cooling, the excess material (known as “flash”) is trimmed or cut away, leaving the finished product.
Pressure thermoforming is used to create a wide range of products, from simple packaging trays to more complex items like automotive components, aircraft interior parts, and medical device housings. This process is often chosen for its ability to produce parts with excellent detail and surface finish, making it a cost-effective option for manufacturing items with intricate designs and aesthetics. Additionally, it is suitable for both small and large production runs, offering versatility in production quantities
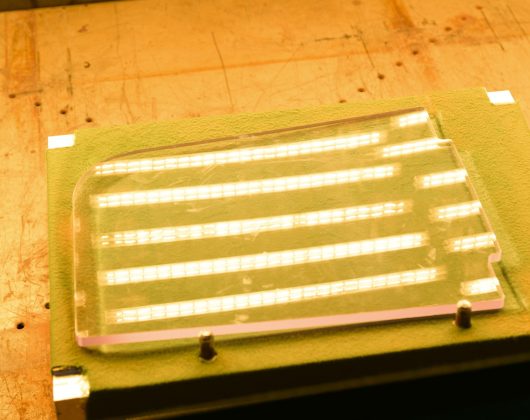
Benefits for pressure thermoforming
Applications
- Automotive parts
- Light covers
- Machine guards
- POP & Kiosks
- Helmet Visors
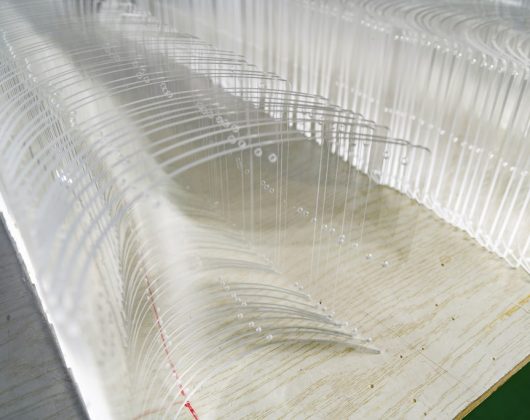
Mechanical Thermoforming
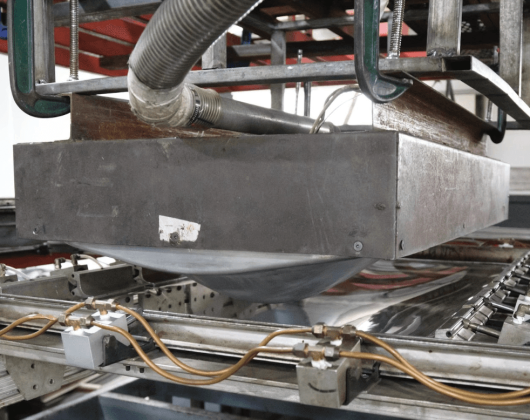
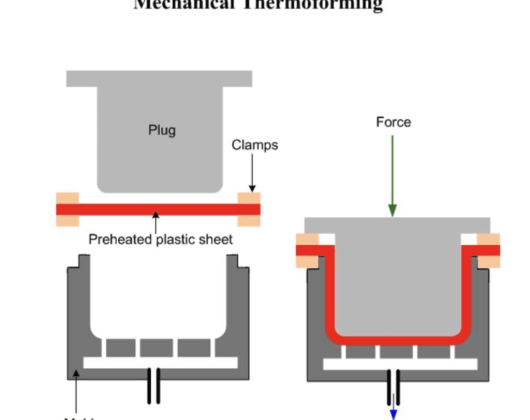
Drape Forming
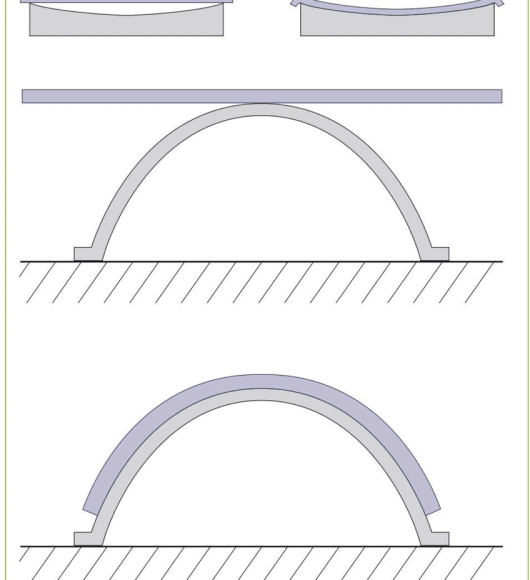
Benefits of drape forming
- Better versatility
- Maintains consistent thickness
- Option for clear parts
- Ideal for large sizes
- Low-cost tooling
Production runs can range from 1 to 1000
Drape forming is a suitable solution for large-sized polycarbonate panels, and it works well with both thin gauge and heavy gauge polycarbonate sheets.
This method allows for rapid production of your parts – for example, creating a curved, clear display window or dome, helmet visor, polycarbonate skateboard, or polycarbonate police shield. For projects with small quantities, drape forming is an excellent way to start. You don’t have to invest a significant amount for your mold compared to vacuum forming.
Applications of drape forming:
- Acrylic Cylinders (made with one or two vertical seams)
- Light covers
- Curved window panels
- Signage
- Skylight domes
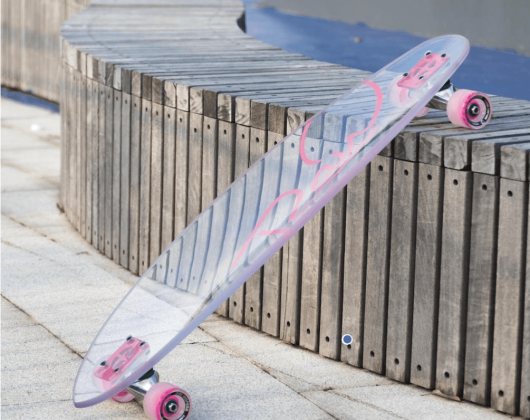
Polycarbonate drape forming temperature
Blow forming plastic
Benefits of blow forming plastic
- No tooling fee or very inexpensive tooling fee
- Tools can be made quickly
- Production can run small quantities
- Free-blown parts have no mark-off
Applications of blow forming plastic
- Skylight domes
- Acrylic domes
- Giant polycarbonate bubble dome
- Plastic domes
- acrylic globe, acrylic hemisphere
- Giant snowglobes
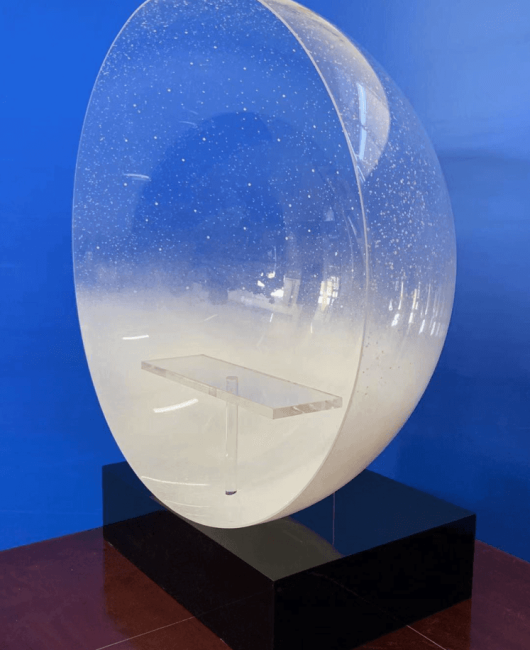
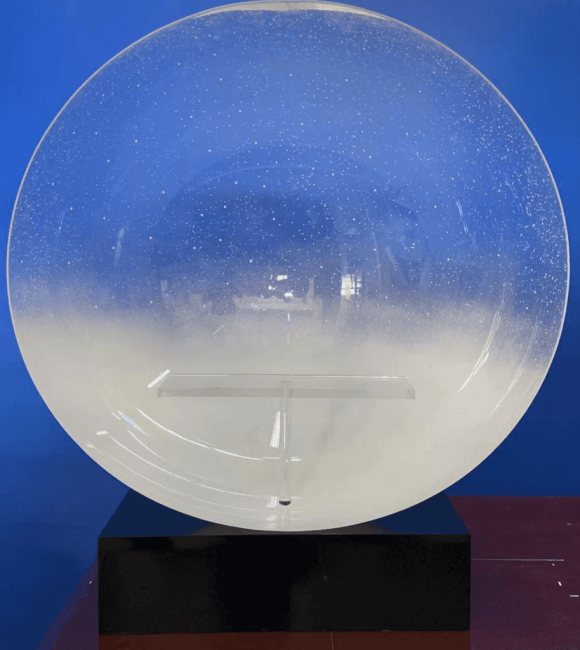
Polycarbonate Heating and Cooling
Conclusion
Get A Quote Today
Bring Your Ideas to Life with Excelite Plastics.
Custom Polycarbonate Solutions Tailored for You.
Share Your Project With Us!
+86 135 8555 4902